ABSTRACT
In this study, brine derived from the Dead Sea has been used as a chloride source (electrolyte) in the electrochemical production of active chlorine (AC) compounds. Due to the high salinity values of its brine, the Dead Sea is the saltiest water in the world due to its salinity value of about 30%. The rate of electricity consumed to produce AC when using Dead Sea brine electrolyte was found to be about 35–45% of the rate used to produce the same amount of AC from 40g/l NaCl electrolyte. The generation rate of AC from Dead Sea brine was significantly higher than that from the NaCl electrolyte; it increased by 95% after 20min electrolysis. The decrease in the AC generation rate and increase in the rate of electricity consumed with time occurred due to the accumulation of deposits on the electrodes. Circulating the brine with high velocity through the electrolytic cell alleviated electrode deposits. The optimum process parameters namely anode current density and ratio of electrolyte volume to cell volume were found to be 1200A/m2 and 10–15, respectively. The presence of Ca++ and Mg++ in Dead Sea brine increased the disinfection efficiency of the generated AC in comparison to the disinfection efficiency of AC generated from the NaCl electrolyte.
Keywords: Dead sea; Anode; Active chlorine; Electrochemical
1. Introduction
Interest in the on-site electrochemical generation system of active chlorine (AC), such as Cl2, HOCl, and OCl , has developed due its safety, high disinfection efficiency, and ease of operation [1]. Electrochemical generation of sodium hypochlorite by the electrolysis of sodium chloride solutions is the most widely used method and has been studied by many researchers [2–8] Sodium chloride has been used as a
chloride source due to its availability and low-cost comparison to other reagents. The effect of adding
other chloride sources (chlorides of calcium, aluminum, and ferric) to sodium chloride electrolytes on the generation rate of AC has also been investigated [2,9]. The results have demonstrated that the addition
of calcium chloride in ratios up to 25% enhance both disinfection and current efficiencies of the produced
AC. The feasibility of adding aluminum and ferric chlorides to sodium chloride electrolytes for the purpose of combining water disinfection and coagulation has been proved [2,9]. Sea water, which is an abundant source of chlorides Cl (19.5g/l), has been also used as an electrolyte in the process of electrochemical generation of AC [1,10–13]. On-site generated AC from direct electrolyses of sea water is being used to treat sea water from algae and prevent micro-organ
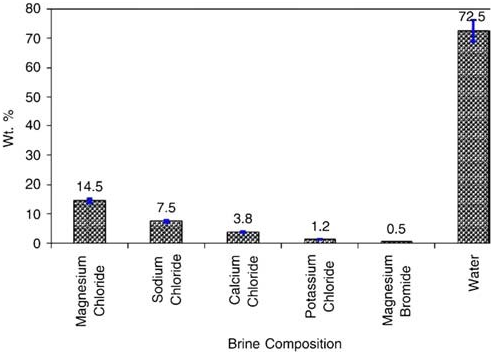
Fig.1.DeadSeacomposition
ism growth in sea water at a desalination plant located in the industrial city of Yanbu [14,15]. In another study, it was found that using sea water as an electrolyte enhanced the AC generation rate and,
consequently, the disinfection efficiency [16,17]. The use of sea water as an electrolyte has the advantage tobe inexpensive; however, the scale formation on the electrodes is the main disadvantage. Different methods are currently being used to remove the scales from the cathode surface such as acid cleaning, use of high fluid velocity through the electrolytic cell, and inversion of electrode polarity. Chloride ions (Cl ) concentration in the Dead Sea brine is about 225.5g/l,being about 11.5 times that of sea water, which is
19.5g/l. Overall Dead Sea brine is over nine and a half times more saline than ordinary sea water [18].
Henceforth, it is unfavorable for fish habitats and most other aquatic life due to the high salinity values
of its brine, being by far the saltiest water in the word with a salinity value of about 30% [18]. The mineral
content of the Dead Sea is significantly different from that of ocean water, consisting of approximately 52% magnesium chloride, 28% sodium chloride, 14% cal cium chloride, 4% potassium chloride, and 1.7% magnesium bromide with the remainder comprising of various trace elements. The average density and salinity of Dead Sea brine are 1.2376g/cm3 and 337.73g/l, respectively [18]. General composition of Dead Sea brine is given in Fig. 1 [19,20]. The main objective of this research is to explore the optimum parameters of the electrochemical generation of AC from the Dead Sea brine. To prevent or reduce scale formation on the cathode surface, the brine will be pumped and circulated through a pressurized electrolytic cell with high velocity. The main process parameters are: anode current density, volume of circulated brine (electrolyte),and circulation (electrolyses) time.
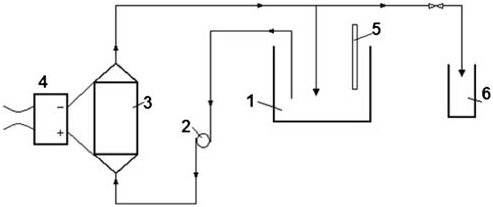
Fig. 2. Laboratory set-up: (1) Electrolyte vessel; (2)Peristaltic pump; (3) Electrolytic cell; (4) Rectifier; (5)Thermometer; and (6) Sampling glass.
2. Materials and methods
Dead Sea brine was simulated in the laboratory by the dissolution of the main salts in distilled water and
used as an electrolyte in the electrochemical process of AC generation. Experiments were conducted using a laboratory setup as illustrated in Fig. 2. The setup consisted of a vessel for the Dead Sea brine (electrolyte), a circulation pump, and a pressurized electrolytic cell connected to a Franell AP (100V to 90A)rectifier. The brine was circulated through the electrolytic cell with high velocity to remove the scales from the cathode surface. The brine was pumped from vessel (1) by peristaltic pump (2) through cell (3) and screen (4) to vessel (1) again. Samples were collected with 15min intervals in glass tube bottle (7) to determine AC concentration and pH value; a continuous monitoring of electrolyte temperature was accomplished by a thermometer (6). The cell (Fig. 3) was made of a tubular vertical stainless steel cathode with a diameter of 0.06m and height of 0.08m, bounded by two perforated plates from the upper and lower sides. A vertical granular tubular titanium anode coated with nickel oxide with a diameter of 0.04m was welded to the lower plate coaxially with the tubular cathode welded to the upper plate. A stainless steel rod with a diameter of 0.02m acting as a second cathode was also welded to the upper plate, passing inside the tubular anode. A granular anode surface was used to increase the contact area between the anode and the electrolyte in order to increase the process efficiency. The selection of titanium anode was due to its high chemical and mechanical resistances. The cell is connected to a DC power through the lower and upper perforated plates which are connected with the electrodes. The electrolyte enters the cell from an influent pipe through the lower perforated plate and leaves through the upper perforated plate to the effluent pipe. The work volume of the electrolytic cell is 0.000232m3, anode surface area is
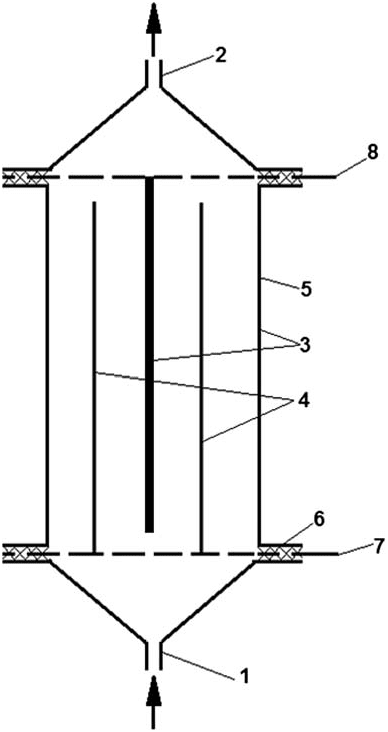
Fig. 3. Electrolytic cell: (1) Influent pipe; (2) Effluent pipe(3) Cathodes; (4) Anode; (5) Cell external body; (6)
Isolation rubber; (7) Anode connector to power supply;and (8) Cathode connector to power supply.
0.023m2, and the gap between the electrodes is 0.1m. To determine the optimum anode current density,
experiments were conducted using an electrolyte volume of 2l, and the anode current density was altered
in the range of 400–1300A/m2. The optimum electrolyte volume to be circulated through the cell depends on the volume of the cell; therefore, the ratio of total electrolyte volume to the volume of electrolytic cell Vtot/Vcell was introduced as the circulation coefficient K. To determine the optimum K value, experiments were conducted using the predetermined optimum anode current density of 1200A/m2 and K values of 4.3, 8.6, 12.9, and 17.2 which represent electrolyte volumes of 1, 2, 3, and 4l, respectively. The concentration of AC was determined, and the electrolyte temperature T (˚C) and pH were recorded after every 15min. The measurement of AC concentration was carried out according to the standard methods [21]. All experiments were duplicated, and the results were presented as mean values with deviations of less than 5%. The mass of AC (MAC) in grams was calculated as the product of AC concentration (CAC) and electrolyte volume. The generation rate of AC (G) and the rate of consumed electricity per kilogram of generated AC (P) have been calculated using the following equations:
G=60Mac/t
where G signifies the generation rate of AC, g/h; t signifies the circulation time, min; and MAC signifies
the mass of AC, g.
P=VIt/MAC
where P signifies the rate of consumed electricity, kWh/kg; V signifies the voltage between electrodes; I
signifies the current, A; t and MAC signify as previously defined.
To maintain a constant anode current density of 1200A/m2, the voltage between electrodes was changed in the range of (3.8–4)V. Similar experiments were conducted in the same laboratory setup using a
NaCl electrolyte concentration of 40g/l. The rate of electricity consumed and the rate of AC generated
from both Dead Sea brine and NaCl electrolytes were compared.
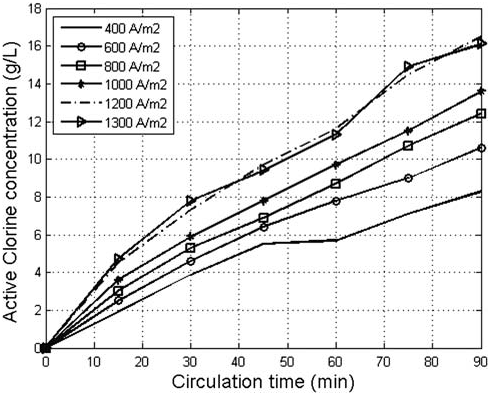
Fig. 4. The effect of anode current density and circulation time on the concentration of the generated AC
3. Results and discussion
The concentrations of AC as a function of circulation time at various current densities are shown in
Fig. 4. It can be seen that AC concentration nonlinearly increased with the increase of circulation time and
current density at all applied current densities. The obtained results are similar to the results reported by
[6,22] . They found that during the electrolysis of highly concentrated electrolytes, part of chloride ions
did not oxidize to form AC due to the limited reactive surface of the anode and the reduction of AC on the cathode. It was also noticed in Fig. 4 that AC concentration did not increase significantly when the anode current density increased from 1200 to 1300A/m2 and, therefore, the optimum anode current density was considered 1200A/m2. The results presented in Fig. 5 indicate that the lower the K value, the higher the concentration of the produced AC with time. However, when electrolytes of a low K value (4.3) was used, a more rapid increase of electrolyte temperature with time was observed in comparison to the temperature of electrolytes of higher K values as shown in Fig. 6. High temperature promotes the oxidation of AC to chlorate and reduces chlorine solubility in the electrolyte which subsequently decreases the increasing rate of AC formation [9]. Despite the abundance of Cl ions in the electrolyte, equilibrium between AC formation and conversion to chlorate was reached after 60min of electrolysis when electrolytes with a K value 4.3 were used. Due to the slow increase in the temperature of high K value electrolytes, the time required to reach the equilibrium between AC formation and conversion increased. The mass of the gene
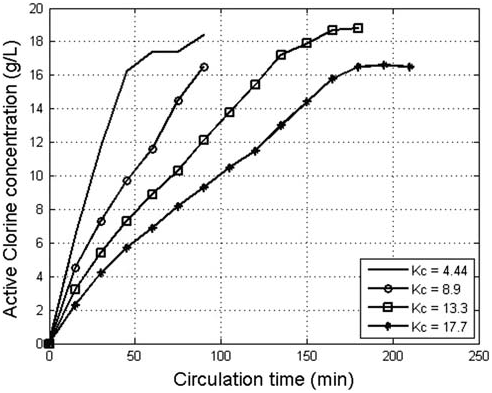
Fig. 5. The effect of circulation coefficient on the concentration of the produced AC.
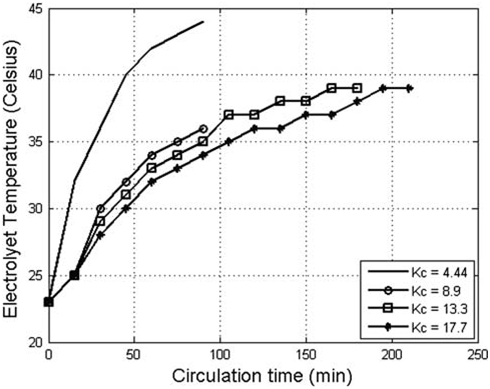
Fig. 6. The effect of circulation coefficient on the temperature of the produced AC solution.
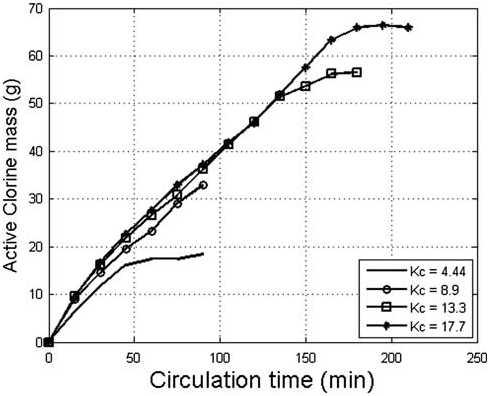
Fig. 7. The effect of circulation coefficient on the mass ofthe produced AC.
ated AC increased proportionally to the circulation time up to 100min for K values of 8.6, 12.9, and 17.2
(Fig. 7). It is obvious that the increase in K values beyond 12.9 did not cause an appreciable increase in
the AC mass during electrolyses with a time up to 135min, therefore the optimum K value can be consid
ered to lie in the range 10–15. These results comply well with the results of AC generation from electrolytes concentration of 40g/l as NaCl with a current density of 800A/m2 which were conducted at the same laboratory setup. The change in the pH value of electrolytes of different K values with time is presented in Fig. 8. After an electrolysis time of 15min, the pH increased linearly from 5.65 to 6.5, 6.8, 7.7, and
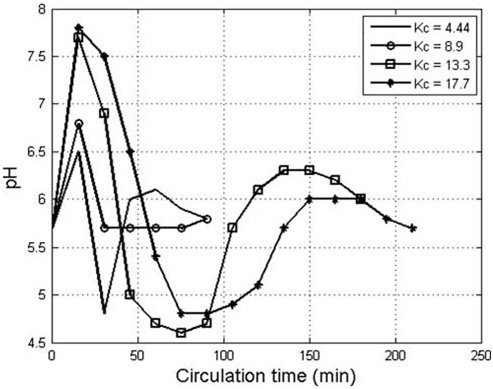
Fig. 8. The effect of circulation coefficient on the pH of the produced AC solution.
7.8 for K values of 4.3, 8.6, 12.9, and 17.2, respectively, due to dissociation of water molecules and accumulation of OH ions in the cathode zone and diffusion in the bulk of electrolyte. A rapid decrease in the pH value took place due to the consumption of OH ions in reaction with the magnesium and calcium cations present in the electrolyte to form insoluble calcium and magnesium hydroxides as shown below:
After the consumption of the main mass of Ca and Mg ions present in the solution by the above reactions, the pH value increased uniformly with time to reach a constant value of 6–6.2. The optimum parameters of electrochemical AC generation using NaCl electrolytes namely NaCl concentration, anode current density, electrolyte volume (K) value, and circulation time were found to be 40g/l, 800A/m2, 10–15, and 40min, respectively. The results presented in Fig. 9 illustrate the generation rates of AC from Dead Sea brine and NaCl electrolyte using the optimum parameters, where it can be seen that the AC generation rate from Dead Sea brine is significantly higher than that from NaCl electrolyte, and it is increased by 95, 55, and 54% after 20, 40, and 60min, respectively. The presence of Ca++ and Mg++ cations beside the abun dance of Cl ions in the Dead Sea brine caused deposit formation on the cathode surface, consisting mainly of Ca(OH)2 and Mg(OH)2. The formation of a thin film of these deposits on the cathode surface at the beginning of electrolysis reduced the reduction of
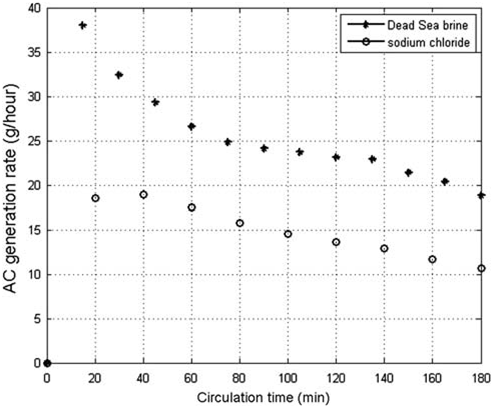
Fig. 9. Comparison between AC generation rate from DeadSea brine and from sodium chloride electrolyte
concentration of 40g/l.
hypochlorite ions at the cathode, causing a high increase in the AC generation rate. However, the
gradual increase in the thickness of this film with time caused a gradual decrease in the generation rate due to limiting the reactive surface at the anode and increasing the electrolyte temperature. Moreover,
when the deposit film thickness increased on the cathode, the electrical resistance increased and the energy efficiency decreased. Therefore, the rate of consumed electricity and the electrolyte temperature increased with time. Due to the high salt concentration and the abundance of Cl ions in the Dead Sea brine, the rate
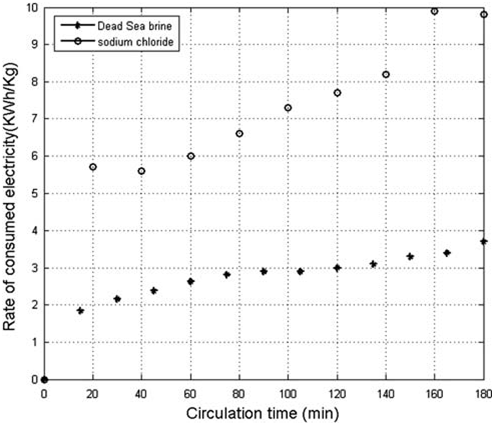
Fig. 10. Comparison between rates of consumed electricity per kilogram generated AC from Dead Sea brine and from sodium chloride electrolyte concentration of 40g/l.
of energy consumed was significantly lower than the rate of energy consumed when NaCl electrolyte was
used (Fig. 10). During 100min of electrolysis, the rate of electricity consumed to produce 1kg of AC from
Dead Sea brine is about 35–45% of that required to generate one kilogram AC from NaCl electrolyte.
Taking into account the cost of both NaCl salt and the energy for its dilution in addition to the energy cost required for AC generation, the use of Dead Sea brine as an electrolyte is highly feasible. Moreover,
according to the results obtained by [9], the presence of Mg++ and Ca++ cations should increase the disinfection efficiency of AC produced from Dead Sea brine.
4. Conclusion
Use of Dead Sea brine as an electrolyte decreased the rate of electricity consumed in electrochemical
production of AC by 35–45% in comparison to the use of NaCl electrolyte with a concentration of 40g/l. The high concentration of Cl and presence of Ca++ and Mg++ in Dead Sea brine not only increased AC generation rate but also increased its disinfection efficiency. The high velocity of the circulated brine through the electrolytic cell alleviated the problem of deposit formation on the cathode surface. The optimum process parameters namely current density and the ratio of electrolyte volume to the volume of electrolytic cell are 1200A/m2 and 10–15, respectively.